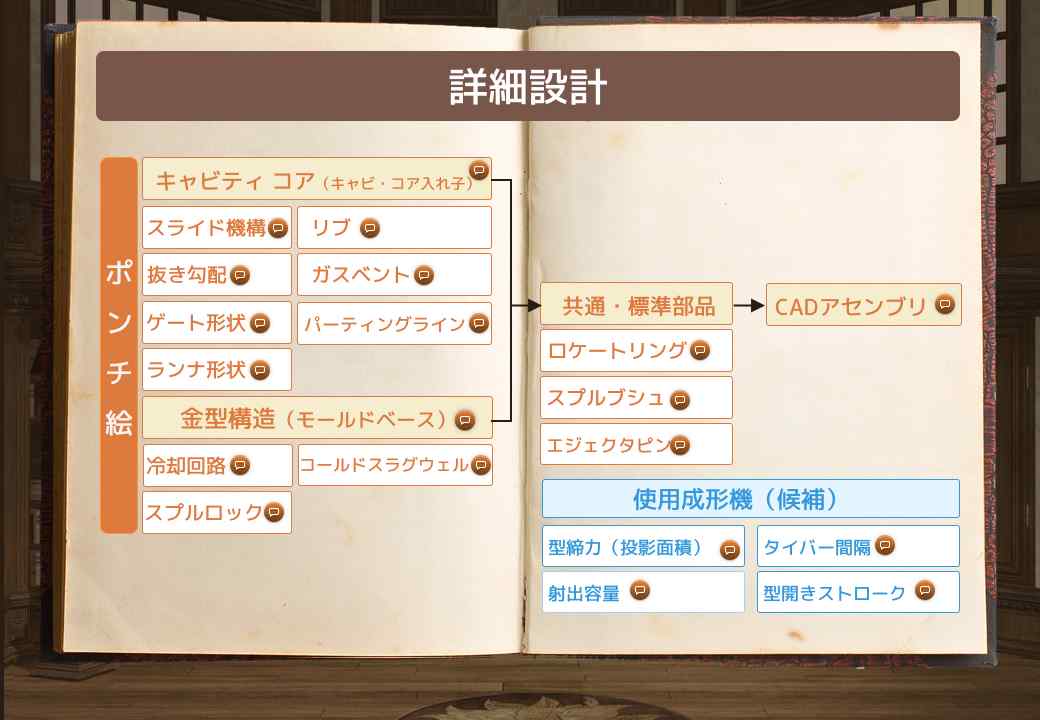
キャビティ部はみがき作業やシボ加工など、完成まで時間がかかるため設計・加工を優先させます。
今回は入れ子方式でしたので、キャビ・コア部品のモデリングを行います。(モデリング手法についてはここでは触れません。)
スライド機構は、金型のアンダーカットを成形する部分を外すための仕組みです。
アンダーカット処理が必要であれば、ポンチ絵でスライド機構を検討しています。
新人の金型設計者の場合、いきなりポンチ絵を描くのが難しいので、最初はベテラン設計者がポンチ絵を作成し、新人がそのポンチ絵を使ってCADによる金型設計を行います。このようなベテランと新人の分担作業を半年から1年かけて新人教育を行います。
新人設計者からベテランへ質問が増えてくれば、新人が成長している証拠です。そういった質問の中から、ベテランが新たな機構の改善方法に気づくこともあり、お互いにメリットはあります。
今回のハンドスピナーでは、本体の外周は抜き勾配はありますが、中心部はベアリングを挿入するため、抜き勾配はありません。この場合樹脂の収縮によって離型しづらくなりますがエジェクタピンを多めに配置することで、確実に離型させます。
シボ加工をする箇所は表面の凹凸が抵抗となって離型しづらくなるため、抜き勾配を大きくする必要があります。金型設計者からすると3度から5度くらいの抜き勾配を必要としますが、抜き勾配が大きくなるとデザイン性が損なわれる場合があります。しかし、シボの種類によっては、抜き勾配の角度は1度、2度でも離型が可能な場合もあります。デザイン性も考えながら、シボ加工業者にアドバイスをもらい、設計段階で失敗を回避できれば一人前の「型技術者」と言えます。
ゲートにはいくつか種類があります。ピンゲートであれば金型構造はスリープレートになりますが成形工程でゲートと製品が離れて出てくるので、後作業が楽になります。プラモデルで見るのはサイドゲートです。説明書と成形品を見比べながら自分でニッパーを使って切断します。デザイン性を重視し、ゲート痕を見せたくない場合には、サブマリンゲートにし、外観から見えないようにします。サブマリンゲートは加工工程が複雑になることが多く、金型コストは上がります。
ゲートサイズを小さくすれば、ゲートシール時間の短縮になる反面、キャビティへ樹脂が流れにくくなります。その対処法として樹脂の温度や射出速度を上げますが、反面ガス焼けなどの成形不良も発生するため、キャビティ内の空気・樹脂から発生するガスを排出するためのガスベントが重要となります。優れた金型設計者になるためには、ガスベントをどの位置、大きさで配置するかを学習しておきましょう。
金型に配置した成形品に、樹脂を行き渡らせるための道をランナといいます。
一度にたくさんの製品を成形する多数個取りなどの場合、金型へ成形品をレイアウトしていきますが、それを結ぶようにランナを配置していきます。成形品へのゲート位置は製品設計者と事前に決めるので、レイアウト作業が重要になります。
CADを使って設計し、樹脂の流れをシミュレーションで確認します。キャビティ内の樹脂の充填が均一に終わり、保圧作業になるようランナの長さ・太さを調節して「同時充填・同時保圧」が理想です。
ランナーは円形の方が、流動性に優れますが、キャビ・コアの部品とも半円形状の加工をする必要があるため加工時間が増えてしまいます。円形以外で良い流動性が得られる形状は、台形で片側のみ加工を行います。
成形品に厚肉のリブやボスがあると、その表面にヒケが発生します。そのためリブやボスはできるだけ薄くします。ボスの強度が必要な場合は肉厚をあげず、リブで強度補強するのがよいでしょう。また一般的にリブの肉厚 t は、成形品の肉厚Tの 0.7 倍未満(t<0.7T)にすると一般にヒケが生じにくくなります。
良い製品を成形するためには、樹脂をキャビティ内へしっかり充填させ、その際に阻害要因となるキャビティ内の気体をしっかりと排出させる「ガスベント」を設けることが必要です。
気体とはもともとキャビティ内に存在している空気や、溶融樹脂によって発生するガスです。気体はキャビティ内で樹脂に押され、逃げ場がなくなると圧縮され高温になる「ガス焼け」という成形不良の原因になります。
ガスベントの位置は、ゲート位置の反対側を基本にしていますが、最近では流動解析の進歩によって最適な位置が求まります。
スライド機構のない単純な構造であれば入れ子を挿入するポケット部や、ロケートリング・スプルーブシュなどの取り付け穴など、定型的なものばかりなので、新人金型設計者はモールドベースの設計から始めるのも良いでしょう。
金型の温度調節や冷却回路は成形作業の安定や成形サイクルの短縮に欠かせません。冷却効果の高い理想的な冷却回路の設計が必要です。
しかし、コスト・納期の面からも金型ごとに大きな違いはありません。
実際にはモールドベースを購入する段階で冷却回路のための穴加工を指定・手配することが可能です。
成形品取り出しについては、スプルーロックピンを使い、金型が開いた時に可動側に成形品が確実に引っ張られることで、可動側にあるエジェクタプレート・エジェクタピンを介して突き出しが可能です。またスプルーロックピンの隙間をガスベントとして利用することも可能です。
射出装置から最初に流れた樹脂の先頭付近は樹脂温度が低くなり、流動性の低下による成形不良の原因になります。そのため、低温となった樹脂をキャビティに充填させないよう、各所に樹脂の溜まり場を設置します。それをコールドスラグウェルといいます。
ロケートリングは成形機のロケートリング穴(固定盤穴)に勘合し、金型と成形機ノズルとの位置決めをするものです。成形機プラテンの固定盤穴にロケートリングをはめ合わせることにより、金型と成形機ノズルとの位置決めがされます。ロケートリングは一般的に、市販品を用います。
スプルーは成形機ノズルと金型を結ぶ役目をしているため、ノズルとの接合時による摩耗や損傷などが起こります。そのため、スプルーは金型に直接彫り込まず、スプルーブシュとして別に加工したものを挿入、交換可能とするのが一般的です。
スプルーブシュ入口の穴径は成形機のノズル径によって決まり、ノズルタッチ部の R も成形機ノズル先端 Rによって決まります。また、スプルーのテーパは抜きやすいように一般に 1°~4°になっています。
投影面積にキャビティ内平均射出圧力を掛け算したものです。
投影面積はCADデータより算出が可能ですが、キャビティ内平均射出圧力は、プラスチックの種類、成形品の肉厚などによっても異なってくるので正確に見込むことは難しく、キャビティ内平均射出圧力の値は、目安とされている値を使います。
射出容量は、射出成形機のスクリュ断面積とスクリュストロークの積で求められ、成形機仕様の最大射出容量で示されています。そのため選定した成形機の最大射出容量が成形品とランナー、スプルーの合計容量よりも大きくなる必要があり、その値は成形機最大射出容量の 20~80%の範囲にあるのが望ましいとされています。
金型の成形機取り付け作業は、通常天井からクレーンなどで金型を吊り下ろして取り付けるため、金型の横幅寸法がタイバーの間隔よりも小さくなければいけません。
金型の型締状態での全長が成形機の使用金型厚さの範囲内にあるか、また金型の型開きストロークが成形機の最大型開きストローク内に収まっているかどうかを確認します。
型の厚み、スリープレート金型やアンダーカット処理などで型開きストロークが大きい金型は注意が必要です。
金型から成形品を取り出すには、金型を開かなければなりません。この金型の合わせ面をパーティングラインと呼びます。パーティングラインを決めるには、以下の点に注意が必要です。
・目立たないところに設ける。
・単純な形状にする。
・アンダーカットができないように設ける。
・仕上げの容易な位置に設ける。
離型のための成形品突き出しピン
CADとは、「Computer Aided Design」の略で、コンピュータを使って設計することや、設計するためのソフトやシステムのことを指します。このCADを使い金型を設計していきます。現在では、CADなどで作成された設計図面を元に、コンピュータ支援製造 CAM (Computer Aided Manufacturing) で加工プログラムを作成し、工作機械にプログラムを転送して実際の加工が行なわれます。